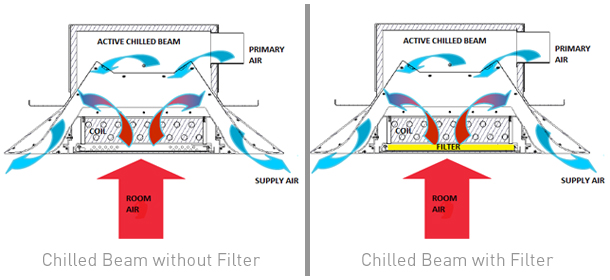
When a mechanical engineer is tasked with developing energy efficient designs, the application of chilled beams is one of the more popular options. Chilled beams have a number of benefits in the right applications; however, local codes and standards can actually impact their effectiveness. Specifically, for healthcare applications in Illinois, codes dictate when HVAC equipment is allowed to recirculate air as well as the filtration requirements for recirculating equipment. This article takes a deeper look at Illinois Department of Public Health (IDPH) filter requirements and how they may affect your next chilled beam project.
First, a basic understanding of this popular system is important. A chilled beam is a type of HVAC system designed to heat or cool large buildings with the use of water. Chilled beams can be active or passive. Active chilled beams have an air plenum and utilize air nozzles to induce airflow from the room across a water coil and back into the space. The velocity of the airflow through the nozzle creates a pressure differential which pulls air across the coil. Passive chilled beams are different in that they don’t have an air connection and rely on the buoyancy of air as well as radiant effects to heat or cool the room. Active chilled beams are more effective, and are very similar to perimeter induction units developed and used in the 1980s, but are ceiling mounted and require less air pressure. Like induction units, chilled beams are designed to be non-condensing by utilizing chilled water temperatures that are above the dew point (typically 60-65°F). The chilled beam injects dry and cool primary air (typically 55°F) from the air handling system through nozzles into the room. The nozzles induce room air (typically 75°F) across the water coil where the dry and cool primary air and the cooled room air mix and is recirculated back into the room. The chilled water coil is designed to satisfy the sensible load, and the primary air is designed to satisfy the latent load.
Active chilled beams are designed to recirculate room air through a coil without filtration. It is important to note that there is a chance that the air will condense on the cooling coil. However, there are safeguards in place to prevent condensation from occurring, as well as warning-systems through the Building Automation System (BAS) that alert building management if condensation is occurring. Although chilled beam manufacturers will tell you that this cold and potentially wet coil has very small potential for mold or bacterial growth, in some environments even the slightest risk of mold or bacteria is not acceptable. There are many methods to eliminate or limit the risk for condensation and thereby eliminate or limit the potential for mold or bacterial growth. Regardless, humidity control is required for any design implementing chilled beams (active or passive).
For healthcare applications in Illinois, IDPH code section 250.2480-Mechanical outlines the HVAC system requirements. When equipment that recirculates air is allowed, a minimum efficiency of 30% (approximately MERV 8) filters are required for the following spaces: radiology suite; x-ray diagnostic, fluoroscopy, and special procedures, pharmacy suite, physical therapy suite and hydrotherapy, occupational therapy suite, newborn care unit, surgical suite-operating rooms, and obstetrics suites.
IDPH also dictates that when equipment that recirculates air is allowed, a minimum efficiency of 10% (approximately MERV 1) filters are required for the following spaces: nursing units (including units such as medical, surgical, intensive care, pediatric, psychiatric, obstetric), emergency suites, and outpatient suites. All other types of spaces either do not allow recirculating devices or have no requirement for filtration on recirculating devices.
Because chilled beams recirculate air within the room through a cooling coil, a filter is required when used in the applications listed above. To accommodate this, manufacturers of active chilled beams have developed an active chilled beam with a filter prior to the cooling coil (pictured). This solution seems to satisfy the IDHP requirements and has the added benefit of being easily accessible from the room.
However, there are multiple drawbacks to having a filter prior to the coil on an active chilled beam. First, as the filters load, the pressure drop increases across the filter which restricts the airflow across the cooling coil. This results in less airflow across the coil, which results in less sensible cooling. Second, there is no way to monitor filter loading, so filters would need to be changed on a scheduled basis. Next, the MERV 1 is the lowest quality filter available and only catches large airborne particles such as textile fibers and carpet fibers. The MERV 8 filter catches airborne particles that range in size from 3.0 to 10.0 micron, such as: mold, spores, dust mite debris, cat and dog dander, hair spray, fabric protector, dusting aids, pudding mix, pollen, dust mites, cockroach debris, sanding dust, spray paint dust, textile fibers, and carpet fibers. These filters would be capturing only the relatively large particles that are induced from the room. Likewise, smaller particles can still pass through the MERV 8 filter. These can include legionella, humidifier dust, lead dust, milled flour, auto emission particulates, nebulizer droplets, bacteria, droplet nuclei (sneeze), cooking oil, most smoke and insecticide dust, most face powder, and most paint pigments. A lower MERV number is less effective at filtering the air. Likewise, a higher MERV number is more effective, so it will load quicker and therefore need to be changed more frequently.
A chilled beam without a filter (pictured) will have a relatively constant primary airflow rate and induction airflow rate. Depending on the nozzle design, number of nozzles, and the coil (pressure drop), the chilled beam primary airflow to induction airflow ratio might be 1:2 up to 1:8. This varies between different chilled beam manufacturers. The higher the induction ratio the better the chilled beam performs.
Consider this example: the primary airflow of a 2 x 4 chilled beam is 100 CFM, the induced air is 4x this, or 400 CFM (through the coil). Although the coil is always less area, let’s assume the coil face area is 8 SF (4 x 2). Likewise, the face velocity in this case is 50 FPM. If the filter is also the same area, then a MERV 8 pressure drop will be 0.05” W.C. when it is clean [based on FLANDERS VP-MERV 8, 1 thick pleated filter]. The manufacturer lists a recommended final pressure drop of 1.0” W.C., but this is unrealistic in this case. If the filter is loaded up to 0.25” W.C. (5x clean), then the induced airflow will be reduced from 400 CFM. If the airflow through the dirty filter and coil is reduced down to 180 CFM then the chilled beam coil would provide approximately a 55% diminished cooling capacity. However, the primary airflow cooling effect would remain constant: 100 CFM x 20 degree delta T x 1.08 = 2160 BTU. The cooling coil would start at 2740 BTU with a clean filter, then, as the filter loads as described above, the cooling coil would only provide 1510 BTU of cooling. This equates to an overall cooling reduction of approximately 25%.
Given our example above, a design incorporating active chilled beams should be avoided when filter requirements are present. As the filters load, the chilled beam coil cooling effectiveness is significantly diminished. Hospital and laboratories are generally clean environments, so this filtration seems to add very little benefit.
References:
- “Chilled Beam.” Wikipedia, https://en.wikipedia.org/wiki/Chilled_beam
- http://www.ashraeregion7.org/mississippi/files/ChilledBeams%20(ASHRAE%20Tech%20Session,%20Jackson,%20Mar%202011).pdf
- http://www.troxusa.com/usa/service/download_center/structure/technical_documents/air_water_systems/usa_products/leaflets/PI_012210.pdf
- http://www.trane.com/content/dam/Trane/Commercial/global/products-systems/education-training/engineers-newsletters/airside-design/adm_apn034en_1209.pdf
- http://www.halton.fi/halton/images.nsf/files/4484AC1B37B7861FC2257672007C0081/$file/Halton%20Chilled%20Beam%20Category%20brochure%20en.pdf